Last post went over 3d printer kinematic styles, but in this post I wanted to detail the 3d printer extrusion system and explain the differences between Direct Drive and Bowden styles of extrusion.
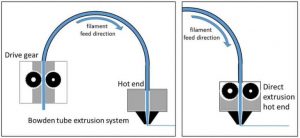
What Are Extruders?
The responsibility of the extruder is to ensure a controlled and accurate feed of filament for printing. This assembly will typically consist of a motor, a driving gear, and an idler bearing. The most important factors to consider for an extruder is the force the extruder can exert on the filament and the placement of the extruder.
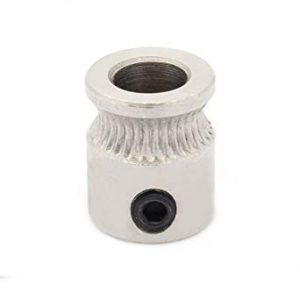
The extruder gear uses a set of teeth to grip filament in order to precisely control how much is extruded. There are a couple different types of these gears, some with a rounder profile (like seen above) and some that are just square across. Jimustanguitar made a cool post here detailing the hold strengths of these different types of gears, worth a quick look over. They are attached directly to the shaft of a stepper motor. This limits the torque to the rating of the stepper motor, usually around 42 N/cm. It is possible to change the torque by using a different stepper motor or using special gear boxes. The other stepper motors that are typically used for extruders are “pancake” style stepper motors that are flatter than a regular stepper motor as well as lighter weight, but apply less torque. or using gear boxes that can be used to increase the torque applied to the filament and increasing motor steps per mm, allowing more precise control.
Another important topic with extruders is extruding flexible filaments. I have seen in many places that Bowden style extruders have a harder time printing flexible filaments than Direct Drive extruders do. This always mildly confused me, but I didn’t think much of it since what do I know, I haven’t printed flexible filaments. In my research I had come across this post by Taylor Landry of MatterHackers detailing extrusion styles. He goes into detail about how both styles of extrusion can print flexible filaments but they need a completely constrained system that doesn’t allow the filament to bend out of the path of extrusion. This post by Matthew Mensley from All3dP reinforces this idea, detailing how this stigma came to be. This post by Tobias Hullette from All3dP starts to contradict this theory, but just suggesting Bowden doesn’t work as well with flexible filaments as Direct Drive does. It seems there is hope for both styles of extruders, but I feel that I am missing something here. I think it’s possible with the right setup, but it may require more research or my own tests. I don’t necessarily plan to print in flexible filament, but I’m sure I could find a use for it.
Direct Drive
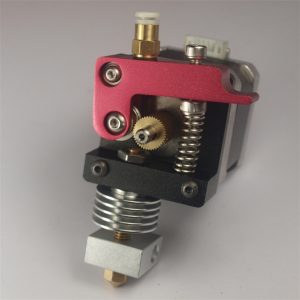
A Direct Drive system is where you have the extruder assembly directly attached to the hotend of the 3d printer.
Advantages
- Less torque needed
- Very responsive retraction
The biggest advantage with a Direct Drive system is the distance between the assembly and the hot end is very small, allowing practically all the torque to be transferred. This puts less strain on the motor over all. This extra responsiveness ensures a very quick and accurate amount of extrusion or retraction when needed.
Disadvantages
- Added weight
- Increased overshoot/slower
The greatest disadvantage of the Direct Drive system is the entire assembly has to be driven by the stepper motors. That added weight causes multiple important problems. This increased weight means the print head has a greater opportunity to overshoot its intended position, skipping steps and resulting in a more inaccurate print. To combat this, we must incorporate more acceleration and deceleration to ensure as little jerk as possible. This results in more complicated settings and an overall slower print speeds.
Bowden
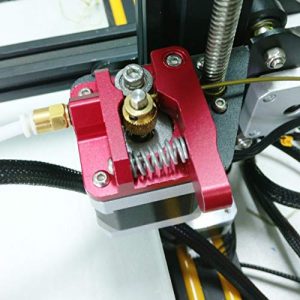
Advantages
- Stationary
- Faster and more accurate print head
The greatest advantage of a Bowden style extruder is in direct contrast to it’s Direct Drive counterpart, the assembly is mounted remote from the hotend. This frees up that weight from the print head, allowing quicker and more accurate acceleration. Since the majority of the print isn’t running at top speeds due to winding paths, the printer spends a lot of time accelerating/decelerating and changing direction. Making these accelerations happen quicker greatly increases overall speed and accuracy in prints.
Disadvantages
- Less reactive/more lag
- More room for error in flexible filament types
The greatest disadvantage in a Bowden style, again in contrast to Direct Drive, is there is a greater amount of space between the extruder assembly and the print head. This makes the extruder a little bit laggy, which can cause some problems in print quality. The most obvious of these is increased stringing.
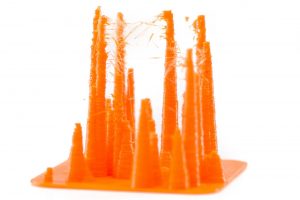
The lack of responsiveness in retraction by the extruder can lag behind the actual movement of the printer. So when the print head moves to a new print location, there is a little bit of material still left on the nozzle of the hotend, dragging and causing this stringing. Therefore, we need to increase retraction settings to ensure the material in completely retracted before moving too much.
Final Thoughts
Both extrusion styles have fair benefits and drawbacks, not making one a more superior option. Instead we have to choose the trade off, greater speed and accuracy in movement or greater retraction accuracy? In my opinion, and looking back to my design goals, I think a Bowden style extruder would benefit me greater with higher speeds and more accurate movement then more robust retraction. If I am able to print flexible filament too, that would be a great plus to this system, but wouldn’t be a huge disappointment. Next posts will be going into the parts I have ordered with a brief overview on their roles and benefits/drawbacks. As of right now I have also gotten all of the aluminum for the frame cut! So I’m super excited to go over that now that all my parts have a home and the full physical printer is being realized. More to come!
Sources
- Alam, Irshad, and pykie23. “Bowden Vs Direct: Quest for the Best 3D Printer Extruder.” 3D Printer Power, 24 Feb. 2019, https://3dprinterpower.com/bowden-extruder-vs-direct-extruder-showdown/.
- “Extruder Drive Gear Shootout.” Instructables, Instructables, 30 Sept. 2017, https://www.instructables.com/id/Extruder-Drive-Gear-Shootout/.
- Hullette, Tobias. “Direct vs Bowden Extruder: The Differences.” All3DP, 26 Nov. 2019, https://all3dp.com/2/direct-vs-bowden-extruder-technology-shootout/.
- Landry, Taylor. “Extruders 101: A Crash Course on an Essential Component of Your 3D Printer.” MatterHackers, 15 Mar. 2016, https://www.matterhackers.com/articles/extruders-101:-a-crash-course-on-an-essential-component-of-your-3d-printer.
- Mensley, Matthew. “2019 3D Printer Extruder Guide.” All3DP, 6 Oct. 2019, https://all3dp.com/1/3d-printer-extruder-nozzle-guide/.